Discover Twenty One Co., Ltd.
All 100 e-book titles are half price! Let’s go find a new you. Spring half-price sale held
Discover Twenty One Co., Ltd. (Headquarters: Chiyoda-ku, Tokyo, President: Naomi Taniguchi) will be open for 28 days from March 1 to March 28, 2023 at 7 online bookstores including DMM.com. We will hold a sale where 100 Discover e-book titles will be half price.
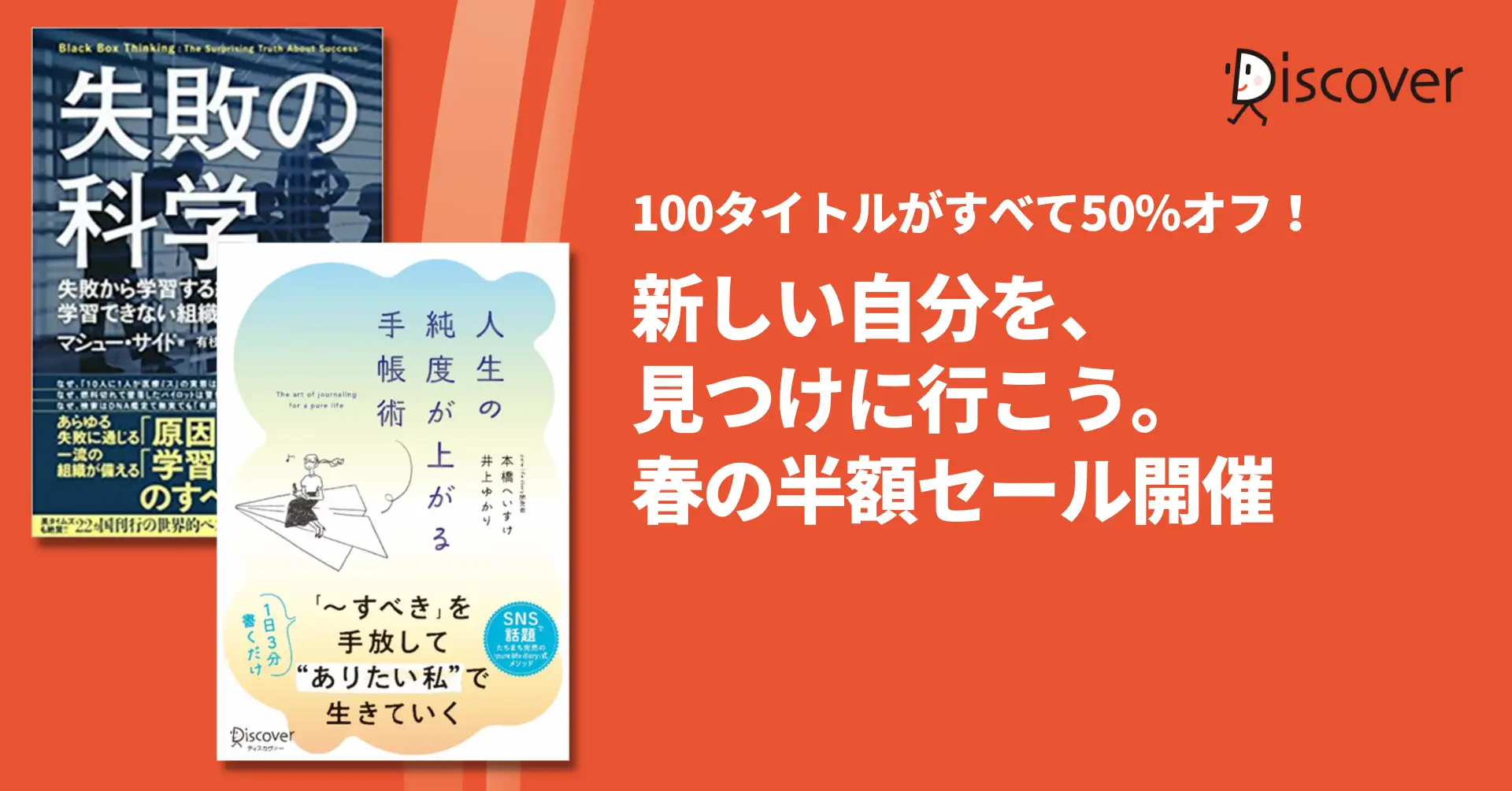
Recommended for new life! Spring half-price sale held
From 3/1 to 3/28, 7 bookstores including DMM.com will hold a campaign where 100 Discover e-book titles will be 50% off.
The world-famous best-seller “Science of Failure”, “Fables that change the way you look at things,” full of small stories, and “Pure life diary”, which became a hot topic on SNS and sold out immediately, is packed with the methods of “The Purity of Life Goes Up.” A wide range of genres of books are covered, including notebook art.
Please take this opportunity to check it out.
[Campaign overview]
Period: March 1, 2023 (Wednesday) to March 28, 2023 (Tuesday) Price: 50% off all items
Target score: 100 points
Target bookstores:
d book
DMM.com
Kinokuniya kinoppy
BOOK☆WALKER
U-NEXT
Google Play Books (*3/2-3/30)
COCORO BOOKS (*3/1-3/26)
Pick up recommended books
1. “Science of failure Organizations that learn from failure, organizations that cannot learn”
Over 50,000 copies! Global bestseller published in 22 countries Why can’t the actual situation of “1 in 10 medical errors” be improved? Why did the pilot who crashed out of fuel “ignore” the warning? Why does the prosecutor insist that he is “guilty” even if he is innocent by DNA test?
Everyone instinctively avoids failure.
That is why only a very small number of people and organizations who actively learn from their failures can demonstrate “ultimate performance.”
In this book, a genius journalist who graduated from Oxford University at the top of his class, along with case studies from all industries, including the medical industry, the airline industry, global companies, and professional sports teams, presents the “causes” that lead to all kinds of failures, and what leading organizations are prepared for. I will introduce the “learning system” that exists. 2. “The fable of sitting right that changes the way you see things”
“Fable” is a tool that conveys life lessons and truths
What image do you have of the words “lesson” and “truth”? Is there a lot of people who feel that it is difficult to approach and that it is difficult?
By taking the form of a story, this kind of “important teaching that is seemingly abstract and difficult to understand” is naturally accepted — that is the “fable”.
This book is a collection of 77 fables that have been handed down from all over the world, including Aesop’s fables, folktales, classics, and anecdotes from around the world, and has commentary on them. In addition to the interpretations that are generally told, the commentaries are arranged so that things can be grasped from multiple perspectives, such as perspectives different from the prevailing theory and modern interpretations.
All fables are summarized so that they can be told within two minutes at the longest, so that they can be used as material for speeches, presentations, etc., as well as to deepen thoughts about one’s work and life. It can also be used as a small storybook when greeting at a company or organization’s morning assembly, or when you have trouble finding “talking material” for your own blog or SNS posting. 3. “Notebook technique that increases the purity of life”
Method to become who you want to be and who you want to be
The theme of this book is “Enhance the Purity of Life”.
To raise the purity of life is to “open your own senses and emotions and live as you want to be”.
By increasing the purity of your life, you will be able to “naturally change into the person you want to be and the person you want to be, and live comfortably” without overdoing it.
This book explains how to deal with the causes of worries and anxieties that serious hard workers tend to fall into, and summarizes how to use a “notebook” to improve the purity of life.
The methods in this book are cognitive science-based and scientifically based. Based on Mr. Heisuke Motohashi’s field experience of coaching and consulting, and Ms. Yukari Inoue’s field of counseling, he asked questions such as, “What kind of words lead to action?” Is it easy to execute?” and so on, and are scattered in the method.
By using the notebook techniques and work in this book, let’s get rid of all “shoulds” and face “what you want to be” and “what you want to be” and refine your sensibilities.